Anodizing is key to finishing parts made from aluminum and other metals.
Anodizing is hugely beneficial if you want high-quality and durable aluminum parts. Because the oxide layer is fully integrated with the material surface, it won’t chip, peel or crack over time. The same can’t be said for paint or powder coating. Anodized finishes have a very long life span thanks to the superior bonding and adhesion of the finish.
Anodizing also hardens the part’s surface up to Rockwell 70C, which ensures the part can handle a lot of use. Because anodized parts are so durable, they don’t often require oiling, conditioning or repainting. Additionally, hard-anodized aluminum is an electrical insulator and serves as a viable insulating material when others prove insufficient.
When you use anodizing to give parts a specific color, these colorants and dyes don’t sit precariously on a flat surface. The coloring agents seep into the hollow pores created by the anodizing reaction. This means that the part doesn’t lose its color to abrasion, wear, UV exposure and other sources of damage. Depending on the type of anodizing you are using, there’s also a wide variety of color finishes to choose from.
On top of these advantages, the process itself is cost-efficient, as is the cost of maintaining the part over its lifecycle. Not only that, anodizing is relatively safe, and produces fewer harmful or environmentally damaging by-products than other finishing processes.
What is anodizing?
Anodizing is a key step in manufacturing CNC machined parts . Anodizing is most common with aluminum, other substrates can be anodized, including magnesium and titanium. An electrochemical process that involves coating a metal part with an oxide surface layer, anodizing gives the part additional sturdiness and a more attractive finish. Anodizing ensures a part can resist corrosion and wear and tear from prolonged use, and that it retains its cosmetic appearance under any conditions.
The most common types of anodizing are Type I (Chromic Acid Anodize), Type II (Sulfuric Acid Anodize) and Type III, also known as Hardcoat. Each type of anodizing is ideal for different materials and serves its own distinct manufacturing parameters. Despite each type’s specific advantages and drawbacks, they all work relatively the same way.
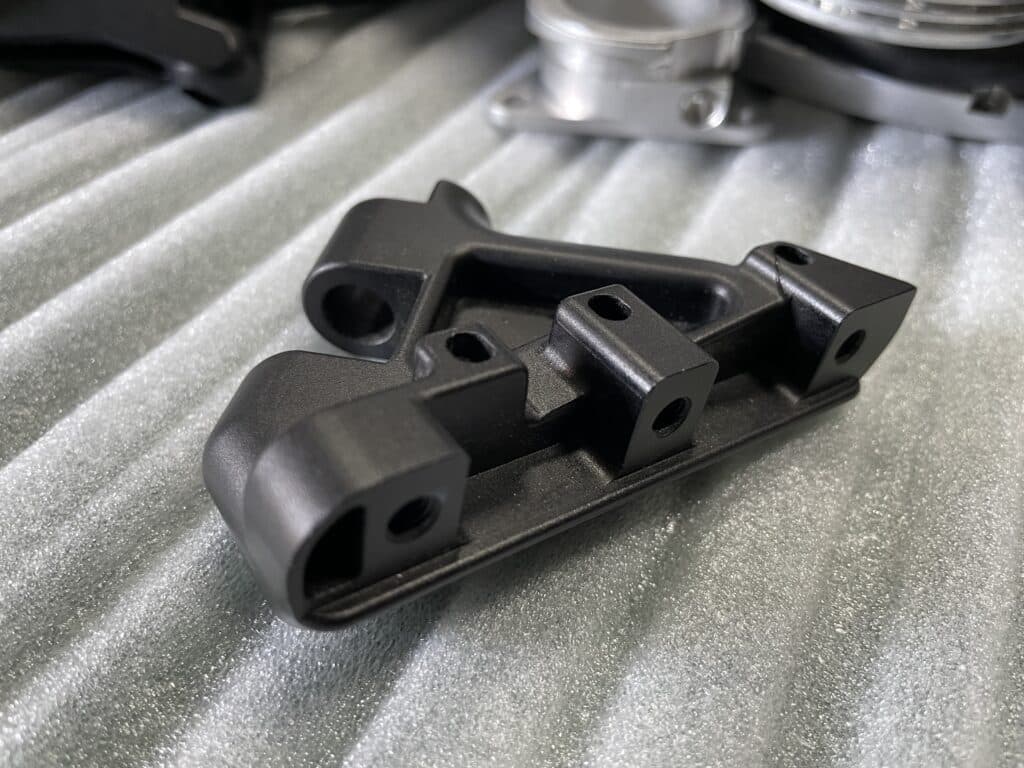
How does anodizing work?
To anodize a part, we should connect it to a positive terminal of an electrical circuit, also called an anode. Then submerge the part in an acidic electrolyte bath solution. This solution contains chemical compounds, such as sodium phosphate, which fill the bath with positive and negative ions.
Once the part is submerged and secured to a hanger so it doesn’t move around, then apply the negative end of the circuit, or cathode, to a metal electrode in the bath. When send voltage through the circuit, the negative electrode attracts positive ions (cations) from the part, and the aluminum part attracts negative O2 ions (anions) from the solution.
When positive aluminum ions leave the part’s surface, it becomes porous, reacting with the negative O2 ions to grow a layer of aluminum oxide.
Let’s break the process down into these simple steps:
1.Turn the part into an anode with a positive charge
2.Turn the metal plates into the cathode with a negative charge
3.Submerge both in the acidic bath
4.Apply voltage
5.Subtract aluminum ions from the part, creating pores
6.Attract oxygen ions to the part’s surface
7.The reaction forms a hard, corrosion-resistant aluminum oxide layer
Add color
You can control the color of the part during anodizing. The wavelengths of the visible spectrum of light, measured in nanometers, can reflect differently depending on the thickness of the oxide coating. Different parameters achieve a variety of colors.
To give your part a bronze or black finish, immerse the part in a solution of metallic salts. These react with the surface to fill the pores with a black or bronze chemical compound. This process is called electrolytic coloring.
If you want another color, you can use dip coloring, which fills the pores with a dye solution. After dipping your part in the dye, place it in heated DI water to halt any further reactions. Dip coloring is the least durable of the coloring options detailed here, as the color may degrade when exposed to UV light over time.
After anodizing, you have to seal the microscopic pores on the surface of the part to prevent further corrosion and improve performance. Without sealing the pores, anodized parts may feel sticky to the touch. As well, open pores can collect dirt, contaminants and stains.
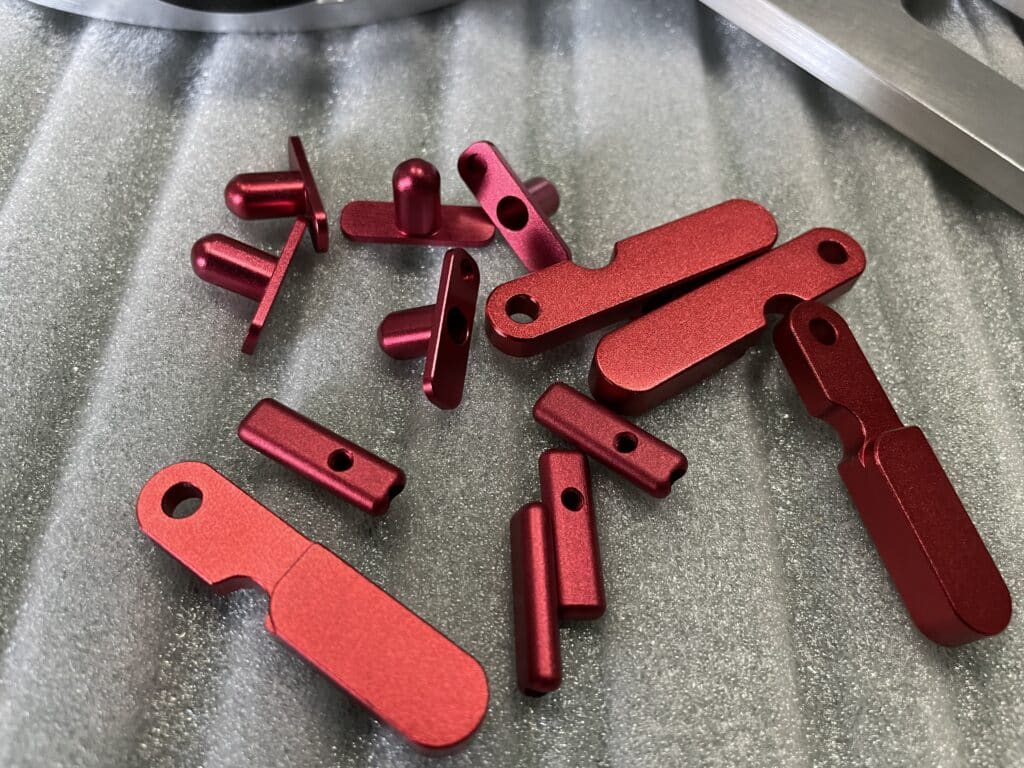
Factor Need to Deep in Mind
Another factor to keep in mind is that the geometric dimensions and tolerances of your part may change with anodization. Anodizing builds up a layer on the part, so remember that when you’re in the design process. As well, anodizing will affect the surface roughness of your part.