- Services
CNC Milling Service
Get custom milled parts for rapid prototyping and production.
Jump to Section
Our CNC milling service is commonly used for:
- functional prototypes
- jigs and Fixtures
- production components in lower volumes
AMPERE FUTURE CNC Milling Capabilities
Our basic guidelines for CNC milling include important design considerations to help improve part manufacturability, enhance cosmetic appearance, and reduce overall production time.We have multiple CNC manufacturing capabilities and can meet a wide variety of needs.
Maximum depth that can be milled is 2 in. (50.8mm) from either side of part.
Size Limit | Metric | Imperial |
---|---|---|
Maximum part diameter | 431mm | 17 inches |
Maximum part length | 990mm | 39 inches |
Maximum swing on carriage | 350mm | 13.7 inches |
Maximum spindle through hole | 40mm | 1.5 inches |
US | Metric | |
Size | 0.25 in. x 0.25 in | 6.35mm x 6.35mm |
Nominal Thickness | 0.040 in. | 1.02mm |
We currently support UNC and UNF threads from #2 up to 0.5 in., and metric threads from M2 to M12. Avoid modeling internal threads on your part design.
Typically, AMPERE FUTURE can hold a machining tolerance of +/- 0.005 in. (0.13mm). Part features are recommended to be thicker than 0.020 in. (0.51mm) in all regions and a nominal part thickness above 0.040 in.
Sharp inside corners on a part will be radiused (rounded) as a natural result of the CNC machining process. Resulting radii will be identified on your quote.
- Hard metals: Minimum width of 0.033 in. (0.838mm) and depth of 0.0118 in. (0.3mm).
- If design permits it, opt for recessed text versus raised
CNC Milling Materials
We stock more than 20 production-grade metal materials that are suitable for various part applications and industries.
- Aluminum
- Brass
- Copper
- Bronze
- Stainless Steel
- Steel Alloy
- Steel Mild Low Carbon
- Titanium
CNC Milling Surface Finishes
Here is a wide selection of metal surface finishing services at your choice for the machined CNC milling parts to improve the part appearance, surface smoothness, corrosion resistance, and other characteristics.
As machined | Description |
---|---|
As machined | Standard finish with a surface roughness of 1.6 μm (126 μin). |
Smoothing | The standard smoothing surface roughness (Ra) is 0.8 μm (63 μin). |
Painting | Spraying paint, pigment, or color to a solid surface as a colored protective layer. |
Passivation | Remove ferrous contaminants or use a light coat of protective material to create a shell. |
Powder Coating | A functional and decorative finish that is applied as a free-flowing, dry powder. |
Anodizing | Type II (anodizing color or clear) or Type III (anodizing hard coat) |
Polishing | Produce a smooth and shiny surface. |
Black Oxide | Forming a black conversion coating on metal parts. |
Bead Blasting | Removing surface deposits by applying fine glass beads at a high pressure. |
Abrasive Blasting/Sandblasting | Smoothing and cleaning a hard surface by forcing solid particles across that surface. |
Electroplating/Plating | Form a thin coherent metal coating on an electrode. |
Brushing | Polishing the metal with grit resulting in a unidirectional satin finish. |
Chromate Conversion Coating | Increase the corrosion resistance while maintaining conductive properties. |
About CNC Milling
CNC milling is a subtractive manufacturing process. It starts by fixturing a block of metal or plastic material inside the CNC mill. Using G-code, the CNC machine is programmed to rapidly mill out parts from the block of raw material. Our 3- and 5-axis CNC machines are equipped with various toolsets to maximize efficiency and production speed.
CNC milling operations include: Plain Milling,Form Milling,Angular Milling,Gear Milling,Thread Milling,Profile Milling,Helical Milling, Cam Milling, Milling Keyways, Grooves and Slot .
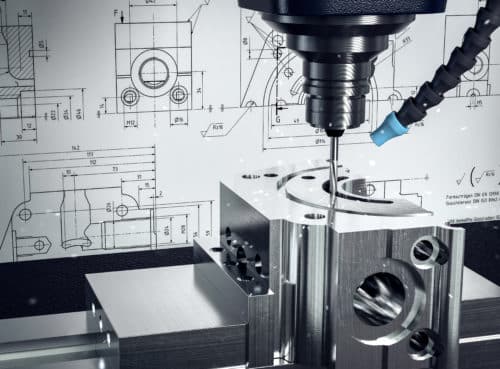